5 Calibrate Dips
The HyDip controller and tank level sensors need to be calibrated for each tank installation. The calibration procedure is a two stage calibration requiring a Low level and a High level measurement. Use the Calibrate menu item to establish these readings as follows:
Select the Low or High value for the relevant sensor, and press ENTER.
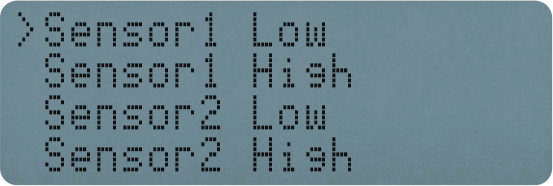
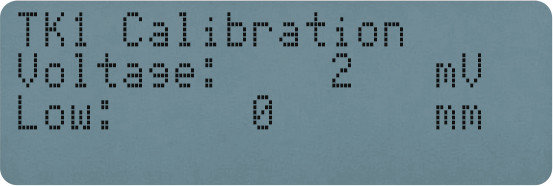
Now depending on the sensor type follow instructions below to calibrate.
Calibrating a hydrostatic (pressure) gauge
Calibration for hydrostatic gauges is a two-part procedure: a zero calibration measured in air (a "Low" level), and a second measured in a known depth of fluid (the "High" level). This means taking a tank level with a dipstick and reading off the depth in mm.
The High calibration is best carried out when the tank is at least 60% full. If the tank level is too low to provide an accurate calibration, you can use a nominal calibration factor, or wait to take a more accurate dip for the High level after the first tank fill. When you update the High level figure you can use the menu on the controller device or the online website control panel.
- Select the Low value for Sensor 1 on the menu. The first two lines on the HyDip display will show the sensor number and the level in mV. The third line is where a depth in mm should be entered using the keypad (see image below).
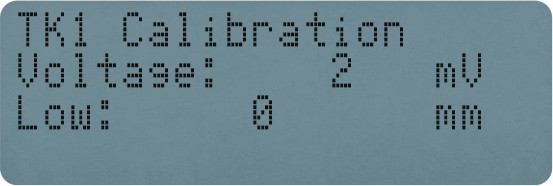
- To set the Low level, remove the sensor from the tank and suspend it in air. Once the mV output value shown on the HyDip controller is stable, type in a value in mm.
Adjust for the gauge "dead band"
The Low Level may not be at 0mm. The actual measure point of a hydrostatic sensor is usually a few millimetres above the bottom of the gauge; see the manufacturer’s data sheet to confirm this distance from the physical gauge bottom to its measure point, and type it in as the Low in mm.
If the sensor is to be positioned at a level below the bottom of the tank, e.g. tapping into an outlet pipe below the tank, use the down arrow to enter a negative offset value in mm equal to the distance below the bottom of the tank.
- Press ENTER.
- Next select the High value for the same sensor.
- Take a manual dip of the tank in millimetres using a dipstick, then lower the hydrostatic sensor probe to the bottom of the tank. Type in the measured value. Use the < and > keys to move across digits if required. To ensure the calibration is accurate wait until the voltage level is stable; this time can vary between different gauge manufacturers.
- Press ENTER.
At this point the controller has the parameters to measure the level of liquid in the tank accurately.
Repeat these steps for all sensors connected to the unit. If no key is pressed within 10 minutes while in calibration mode, the controller returns to the main menu.
Ultrasonic / radar sensor
An ultrasonic or radar sensor sends out a pulse and records the time taken for the echo to be reflected off the surface of the liquid.
Select an ultrasonic or radar level sensor that suits the height of the tank. Manufacturers will normally offer a range of sensors with different maximum tank height specifications.
Some higher quality ultrasonic or radar level gauges can be configured for the actual tank height dimensions Instead of using their factory settings. This will improve gauge accuracy over its full dynamic range. These sensors are typically configured through a PC application provided by the sensor manufacturer.
Locating an ultrasonic gauge
Ultrasonics are particularly sensitive to internal tank obstructions; the signal pulse will reflect off the side of the tank and any internal structures such as bracing, dip tubes, ladders within the focus of the echo. As the tank fluid level is lowered these obstructions become exposed and can cause false echoes, that will make the tank level readings appear higher than the true fluid level.
Where it is not possible to avoid all false echoes in a particular installation, higher quality ultrasonic gauges will normally provide an echo suppression function built into the device.
We've included an example of a false echo suppression procedure for Vega gauges .
Calibrating your sensor
There are several ways to calibrate an ultrasonic or radar sensor. The principle behind all of them is the same. First:
- Measure the distance from the base of the sensor (in position) to the bottom of the tank. Record the distance (in mm).
- Measure the distance from the base of the sensor (in position) to the surface when the tank is full (or as full as possible). Record this distance (in mm).
You now have the mm values for Low and High. If measuring inside is impossible, simulate measurements outside the tank.
Next, take two readings with the sensor following the manufacturer’s instructions (readings may be simulated by aiming the sensor from the correct distance to a solid surface such as a wall):
- Take a reading with the sensor over the empty tank distance. On the Hydip controller keypad, input the Low level value in mm.
- Take a reading with the sensor over the full tank distance. On the HyDip controller keypad, input the High level value in mm.
Magnetostrictive sensor
As with the sensors described above, each calibration is a two-point procedure. Aim to take readings as far apart from each other as possible to maximise the accuracy of the sensor across a range of levels. Full and empty are ideal, but a difference of half a tank full is the least you should allow.
Taking calibration measurements outside the tank
It's most convenient to calibrate the sensor outside the tank, e.g. before fitting it. This can be done on the ground. Simply take a Low reading with the float at the bottom end of the sensor (at 0mm), and a High reading a measured distance up it as close to the maximum level as possible.
Taking calibration measurements inside the tank
If you have to calibrate with the sensor in the tank it's easiest when the liquid level is low (below 40%). Take a dip with the float on the surface and use this measurement when setting the Low reading. Then lift the float to the top of the sensor pole (maximum liquid level) and set the High reading.
If the tank is full (higher than 60%) you can take a dip with the float on the surface to get the High measurement in mm, and find a way to push the float to the bottom of the sensor for the Low measurement (0mm). This is the most difficult and least reliable approach.
Updated 5 months ago